مبانی سیالات تحت فشار و اصول طراحی مدار هیدرولیک
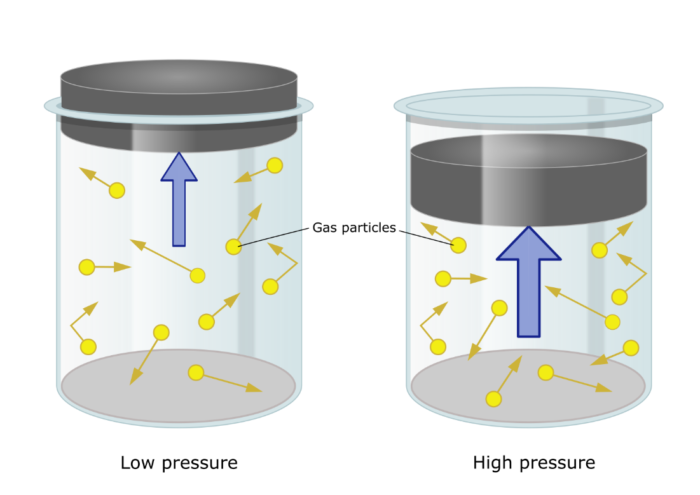
مبانی سیالات تحت فشار و اصول طراحی مدار هیدرولیک: سیستمهای هیدرولیک بهدلیل تراکمناپذیری نسبی سیال، توانایی ایجاد نیرو و گشتاور بسیار بالا در ابعاد فشرده را دارند. از ماشینهای تزریق پلاستیک و پرسهای سنگین گرفته تا فرمان خودرو و تجهیزات هوایی، هیدرولیک همچنان انتخاب اول برای انتقال قدرت دقیق و مطمئن است. در این مقاله، ابتدا شالودهٔ علم سیالات تحت فشار را مرور کرده، سپس گامبهگام وارد ملاحظات ضروری طراحی مدار هیدرولیک میشویم.
2. خواص کلیدی سیال هیدرولیک
خاصیت | اهمیت در عملکرد | محدوده مطلوب در صنعت |
---|---|---|
ویسکوزیته | تعیینکننده افت فشار و راندمان حجمی پمپ | 10–100 cSt در دمای کاری |
تراکمپذیری (Bulk Modulus) | دقت کنترل موقعیت و پاسخ دینامیکی عملگر | > 1.4 GPa |
پایداری حرارتی و اکسیداسیون | جلوگیری از تخریب شیمیایی و لجن | دمای کار < 80 °C و شاخص پایداری بالا |
خاصیت روانکاری | کاهش سایش پمپ و شیرها | افزودنیهای ضدسایش (ZnDTP، فسفاتاستر) |
شاخص گرانروی (VI) | ثبات ویسکوزیته در طیف وسیع دما | VI > 100 برای کاربرد متحرک |
نکتهٔ طراحی: انتخاب سیال با VI بالا امکان استارت در سرما و کار پایدار در گرما را بدون نیاز به گرمکن یا مبدل بزرگ حرارتی فراهم میکند.
3. قوانین پایه حاکم بر سیالات تحت فشار
- قانون پاسکال تغییر فشار وارد بر یک سیال تراکمناپذیر در تمام جهات یکسان منتقل میشود. این اصل هستهٔ تولید نیروی بزرگ با نیروی ورودی کوچک در جکهاست.
- معادله برنولی (صورت انرژی) مجموع انرژی فشاری، پتانسیل و جنبشی در خط جریان ایدهآل ثابت است؛ در عمل، افتهای اصطکاکی و تلاطم باید به آن افزوده شوند.
- اصل بقای جرم (دبی ثابت) و اصل بقای انرژی پایهٔ محاسبات قطر لوله، سرعت جریان مجاز و اندازهگیری خرابیهای احتمالی در سیستم است.
4. اجزای اصلی یک مدار هیدرولیک
رده | مؤلفه | وظیفهٔ کلیدی | ملاحظات انتخاب |
---|---|---|---|
منبع توان | پمپ دندهای، کارتریجی، پیستونی | ایجاد جریان مستمر | فشار نامی، راندمان حجمی، صدا |
واحد کنترل | شیرهای جهت دهنده (4/3)، فشار، دبی | مسیر، سطح و سرعت توان را تنظیم میکند | مشخصات الکتریکی/برقی، زمان پاسخ |
محرکها | جک خطی، موتور هیدرولیک | تبدیل انرژی سیال به حرکت | نیرو، کورس، سرعت، نوع بار |
تجهیزات کمکی | فیلتر، خنککن، اَکومولاتور | پایش کیفیت سیال، ذخیره انرژی و کاهش پیک فشار | β ≥ 1000 برای فیلتر، حجم مناسب اَکومولاتور |
مخزن و لولهکشی | ذخیره سیال و انتقال بدون نشتی | حجم ≥ 3×دبی دقیقهای، سرعت در لوله ≤ 4 m/s |
5. دستهبندی مدارهای هیدرولیک
- مدار مرکز باز (Open Center)
- پمپ جریان ثابت، شیر در حالت بیکاری تخلیه به مخزن
- مناسب برای سیستمهای تکعملگره با نیاز متناوب فشار
- مدار مرکز بسته (Closed Center)
- پمپ دبی متغیر با کنترل جابجایی؛ فشار سیستم ثابت میماند
- پاسخ سریع و امکان تغذیه عملگرهای متعدد بهطور همزمان
- مدار Load-Sensing (LS)
- حس فشار بار و تطبیق لحظهای دبی/فشار؛ تا 30 ٪ صرفهجویی انرژی
- مدار فشار ثابت با شیر کاهنده (Constant-Pressure)
- محبوب در ماشینآلات راهسازی؛ پایداری بالا ولی تلفات حرارتی بیشتر
6. اصول طراحی مدار هیدرولیک
6.1 تعیین بار و مشخصات کاری
- نیروی موردنیاز (F) → ابعاد جک:
A=FPworkingA = \frac{F}{P_{\text{working}}}A=PworkingF - گشتاور موردنیاز (τ) در موتور دوار → حجم جابجایی:
D=2πτPworkingηmD = \frac{2π τ}{P_{\text{working}} η_m}D=Pworkingηm2πτ
6.2 محاسبه دبی و انتخاب پمپ
Q=Av(سیلندر)یاQ=nD(موتور)Q = A v \quad (\text{سیلندر}) \quad\text{یا}\quad Q = n D \quad (\text{موتور})Q=Av(سیلندر)یاQ=nD(موتور)
راهنما: دبی را طوری انتخاب کنید که زمان سیکل با نیاز فرآیند و محدودیت حرارتی سیستم هماهنگ باشد.
6.3 سایزینگ لوله و اتصالات
سیال | حداکثر سرعت مجاز | کاربرد |
---|---|---|
خط مکش | ≤ 1.5 m/s | جلوگیری از کاویتاسیون |
خط فشار | ≤ 5 m/s | کاهش افت اصطکاک |
خط تخلیه | ≤ 3 m/s | کنترل تلاطم |
6.4 مدیریت دما و اتلاف انرژی
- مبدل حرارتی هنگام توان هیدرولیک > 20 kW یا اگر ΔT > 15 °C نسبت به محیط باشد.
- راندمان کل (η_sys) را با جمع راندمانهای پمپ، موتور و هدرولیک لوله محاسبه کنید.
6.5 جلوگیری از آلودگی و الزامات ISO 4406
- هدف معمول: کلاس 18/16/13 برای فشار پایین و 16/14/11 برای فشار بالا.
- فیلتر در خط برگشت + فیلتر فشار بالا برای عملگرهای حساس.
6.6 نمادگذاری و استانداردها
- ISO 1219-1 و ISO 1219-2 برای شماتیکها.
- ISO 4413 الزامات ایمنی، آدرسدهی به Fail-Safe، سرویس و برچسبگذاری اجزا.
7. گامهای اجرایی طراحی (رویهٔ 9 مرحلهای)
- تعریف نیاز و محدودیتهای عملکردی
- تهیه دیاگرام بلوکی جریان انرژی
- محاسبات بار، فشار و دبی
- انتخاب پمپ و عملگر بر اساس Duty Cycle
- طراحی و انتخاب شیرهای کنترل با در نظر گرفتن سرعت پاسخ
- تحلیل حرارتی و تعیین ظرفیت خنککن
- ترسیم نقشهی شماتیک مطابق ISO 1219
- انتخاب حسگرهای فشار/دما و سیستم مانیتورینگ
- ساخت نمونه، آزمون عملکرد و مستندسازی رویه نگهداری
8. نگهداری، پایش وضعیت و عیبیابی سریع
عیب احتمالی | نشانهها | اقدام اصلاحی |
---|---|---|
کاویتاسیون پمپ | سروصدای جیغ، لرزش | بررسی سطح روغن، تمیزی فیلتر مکش |
آلودگی ذرات | حرکت نامنظم عملگر | تست ISO 4406، تعویض فیلتر |
داغ شدن بیش از حد | دمای روغن > 80 °C | افزایش سطح مخزن، نصب مبدل حرارتی |
نشتی داخلی سیلندر | افت فشار در حالت بار | آزمون Drop-Rate، تعویض اورینگ |
Stick-Slip در حرکت | لغزش ناگهانی، ضربان فشار | کاهش اصطکاک، انتخاب سیال با VI بالاتر |
9. نتیجهگیری مبانی سیالات
فهم دقیق خواص سیالات تحت فشار و استفاده از اصول طراحی مهندسی—از محاسبه بار و دبی تا انتخاب فیلتر و استراتژی کنترل آلودگی—بهطور مستقیم بر کارایی، ایمنی و عمر سیستم هیدرولیک اثر میگذارد. بهکمک استانداردهایی چون ISO 4413 و ISO 1219 و بهرهگیری از بهترین رویههای نگهداری پیشگیرانه، میتوان سامانهای ساخت که علاوه بر پاسخ دینامیکی سریع، هزینه توقف تولید را به حداقل برساند.
منابع پیشنهادی برای مطالعهٔ بیشتر
- Esposito, A. – Fluid Power with Applications, 9th Ed. (2024)
- Watton, J. – Fundamentals of Fluid Power Control, Cambridge Univ. Press (2023)
- ISO 4413:2023 – Hydraulic fluid power – General rules and safety requirements
- ISO 1219-1/2:2024 – Fluid power systems and components – Graphic symbols
جهت درخواست و سفارش همه نوع محصولات هیدرولیک، پنوماتیک و ابزار دقیق می توانید از طریق WhatsApp با فروشگاه هیدرولیک و پنوماتیک علی در تماس باشید.